November 20, 2024Components of an Overhead Contact System: Powering Sustainable Urban Mobility
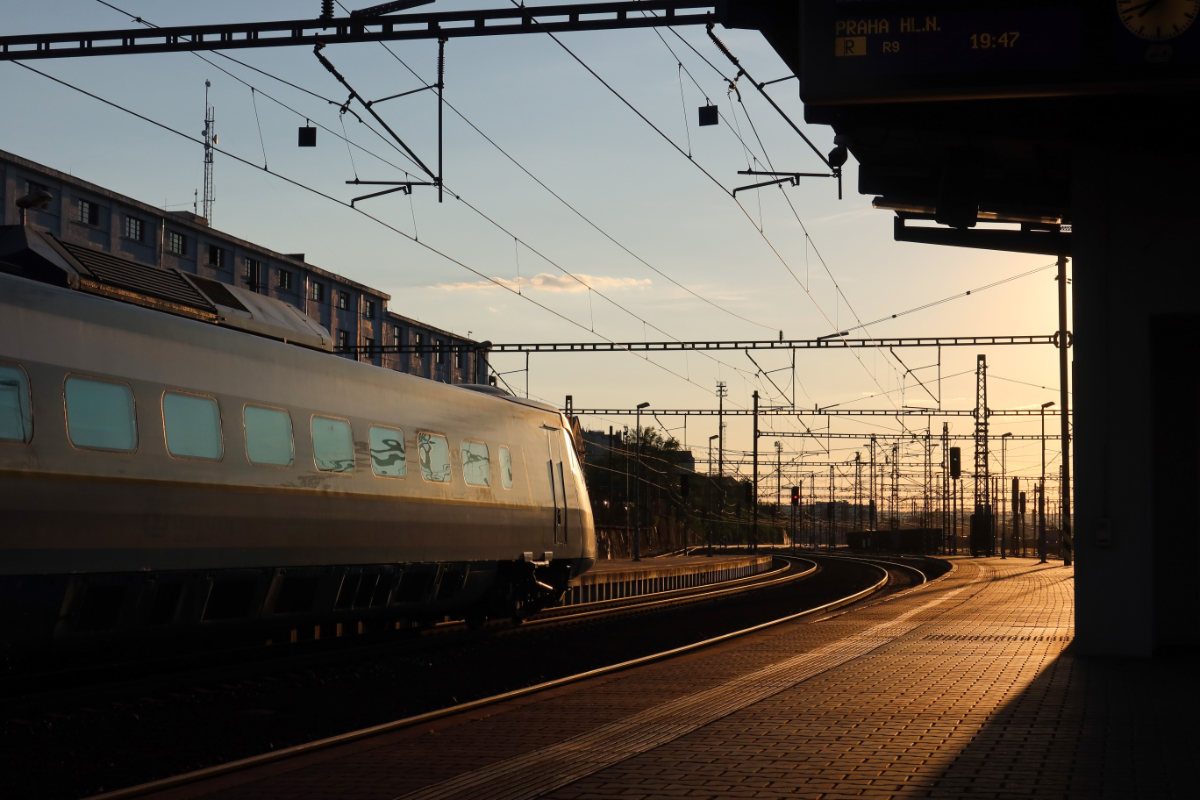
As cities shift toward sustainable transit, Overhead Contact Systems (OCS) stand out as essential infrastructure in electrified mass transit. With advancements in urban transportation, OCS components enable efficient, clean, and high-capacity mobility for railways, light rail, and trams worldwide. At MAC-IMPulse LLC, we are committed to powering this transformation through reliable, made-in-the-USA OCS solutions that energize rail systems from North America to international markets. This article delves into the key components of an Overhead Contact System and their essential roles in advancing electrified transit.
What Is an Overhead Contact System (OCS)?
An Overhead Contact System is a combination of wires, support structures, and hardware that delivers electrical power to trains and other electric vehicles. The system supplies AC or DC voltage through contact wires suspended above the railway tracks, which power trains as they travel along their routes. OCS technology is pivotal to sustainable urban transport, reducing greenhouse gas emissions and reliance on fossil fuels.
Key Components of an Overhead Contact System
The primary components of the OCS include the contact wire, catenary wire, droppers, jumpers, poles and masts, insulators, tensioning devices, regulating equipment, and cantilevers. Each of these components has a specific function, and together, they ensure smooth and continuous power delivery.
1. Contact Wire
The contact wire is the most visible part of the OCS, often seen suspended above rail tracks. It directly supplies power to the train through a pantograph—a device mounted on the train roof that maintains continuous contact with the wire. The contact wire is made from durable materials like copper or copper alloys, designed to withstand constant wear and tear. It’s critical for maintaining high conductivity and allowing efficient energy transfer.
- Function: Provides direct electrical contact to power trains.
- Design Considerations: Requires high durability, low wear, and excellent conductivity.
2. Catenary Wire
The catenary wire, also known as the messenger wire, is positioned above the contact wire and plays a vital role in supporting it. The catenary wire is tensioned to maintain the height and alignment of the contact wire, ensuring that it stays at a consistent height along the track. This prevents disruptions in power transfer, especially at high speeds.
- Function: Supports and stabilizes the contact wire.
- Design Considerations: Strong materials like copper or aluminum, suitable for carrying heavy loads over long spans.
3. Droppers
Droppers are small, wirelike components that connect the catenary wire to the contact wire. They are regularly spaced along the OCS and help maintain a uniform distance between the wires. Droppers prevent the contact wire from sagging or oscillating, ensuring safe and reliable power transfer. They are generally made from lightweight but durable materials, enduring constant vibrations from passing trains.
- Function: Stabilizes the contact wire by securing it to the catenary wire.
- Design Considerations: Lightweight materials, durability under dynamic loads.
4. Poles and Masts
Poles and masts are structural supports that hold the catenary system above the tracks. Depending on the railway’s location, weather conditions, and load requirements, these structures can vary in design and material. Poles and masts are typically spaced at regular intervals along the track and are engineered to withstand environmental stresses such as wind, snow, and temperature fluctuations.
- Function: Provides support for catenary and contact wires.
- Design Considerations: Strong, weather-resistant materials like steel or concrete, stability under various weather conditions.
5. Insulators
Insulators separate live wires from the poles and masts, preventing electrical currents from grounding into the support structures. Insulators play a critical role in safety by ensuring that the electrical power flows only to the train and not into other parts of the OCS or the environment. Insulators must resist high voltage levels and withstand environmental wear.
- Function: Prevents electrical grounding to support structures.
- Design Considerations: High electrical resistance, durable in extreme weather, made from materials like porcelain or polymer.
6. Tensioning Devices
Tensioning devices maintain the correct tension in the catenary and contact wires. This is especially important in regions with temperature variations, as metal wires expand and contract with temperature changes. Without proper tension, wires may sag or lose alignment, interrupting the power supply. Tensioning devices include counterweights and springs, which automatically adjust the tension in response to temperature changes.
- Function: Adjusts wire tension to ensure stable power delivery.
- Design Considerations: Must be responsive to temperature variations, reliable in automatic adjustments.
7. Regulating Equipment and Switching Stations
Regulating equipment monitors the OCS voltage, ensuring a consistent supply of power for safe train operations. Switching stations are positioned along the network to isolate OCS sections for maintenance, troubleshooting, or emergencies without disrupting the entire line. This component is critical for efficient power management and safety.
- Function: Manages voltage and provides power flow control.
- Design Considerations: Integrated with monitoring technology, easy access for maintenance, redundancy for reliability.
8. Cantilevers
Cantilevers are used to suspend and locate the contact and messenger wires over the tracks. They are mounted on the poles and masts using specific components that are designed to meet the structural requirements identified in the design of the OCS. Cantilever construction elements can include insulators, pipe end fittings, and pipe clamps.
- Function: Support, suspend, and locate the OCS over the tracks.
- Design Considerations: Mechanical loads that are imparted by the auto tensioning devices, both vertical and horizontal loads and the environmental loads that are present with certain weather (ice and wind loads).
How MAC-IMPulse Is Advancing OCS Technology
At MAC-IMPulse LLC, we design and manufacture robust OCS components to meet the diverse needs of mass transit systems across North America and the world. Our focus on high-quality materials, precision engineering, and innovation ensures that each component withstands demanding operational environments while contributing to a cleaner, more sustainable future in urban transit. Our commitment to made-in-the-USA products supports local industries and ensures compliance with stringent safety and quality standards.
The Future of Electrified Transit With OCS
Overhead Contact Systems are integral to the future of urban mobility. They support a shift toward greener cities by enabling electric trains, reducing emissions, and decreasing reliance on fossil fuels. Innovations in OCS design—such as advanced materials for durability, smart monitoring systems for efficient power management, and modular components for easier maintenance—are driving the evolution of electrified transit.
As the demand for sustainable and high-capacity transport grows, so does the role of reliable OCS components. MAC-IMPulse LLC continues to pioneer advancements in OCS technology to meet this demand, helping cities worldwide achieve their sustainable transportation goals.
Conclusion
Understanding the components of an Overhead Contact System provides insight into the intricate engineering that powers electric rail transit. Each component, from the contact wire to tensioning devices, is critical in ensuring safe, efficient, and reliable service. As MAC-IMPulse LLC leads the charge in OCS innovation, our products pave the way for an interconnected, cleaner, and more efficient world in electrified mass transit.